Metallurgy, the science and technology of metals, has been at the heart of human progress for centuries. This intricate field involves the study of metals and their properties, as well as the processes used to extract, refine, and manufacture metal products.
From ancient smithing to modern alloy design, metallurgical techniques have continually evolved, making significant contributions to various industries. Today, metallurgy plays a crucial role in manufacturing, contributing significantly to sectors ranging from automotive and aerospace to construction and power generation.
Notably, there are many full time jobs in Pryor, OK, linked to this sector, reflecting its critical importance in local economies. The significance of metallurgy cannot be overstated: it’s the backbone of modern industry. The advancement of metallurgy has spurred growth in various sectors, contributing significantly to technological advancements and economic development.
Modern techniques have enabled the creation of materials with superior durability, performance, and specialized properties essential for industries ranging from construction to power generation.
Applications in the Automotive Industry
The automotive industry has benefited immensely from metallurgical advancements to produce more durable, efficient, and lightweight vehicles. The rise of lightweight materials such as aluminum and magnesium alloys is critical to enhancing fuel efficiency without compromising on strength and safety.
According to WardsAuto, the trend toward lightweight is driven by stringent emission regulations and consumer demand for better performance. This shift towards lighter materials isn’t merely about reducing vehicle weight; it’s about a holistic enhancement of overall vehicle performance. Improved fuel efficiency and reduced emissions are critical in an era where environmental concerns are paramount.
The automotive industry thus leans on advanced metallurgy to produce lighter yet more robust materials that meet safety standards and regulatory requirements. The use of these lighter materials extends the lifespan of vehicles and improves the driving experience by enhancing speed and handling.
Innovations such as high-strength steel and advanced composites further enable manufacturers to design safer, more durable car components, setting new benchmarks in automotive engineering.
Aerospace Engineering Benefits
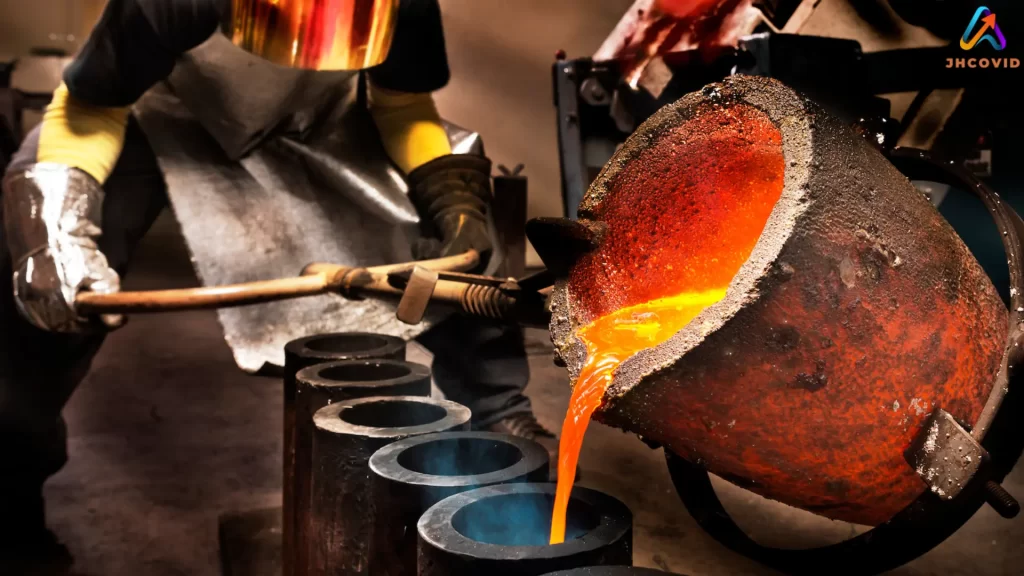
Metallurgy is equally integral in aerospace engineering, providing materials that withstand the extreme conditions of flight, from high temperatures and corrosion to intense mechanical stress. High-performance alloys and superalloys are essential in aerospace, enabling the design and construction of components that are not only lightweight but also exceptionally strong and heat-resistant.
Advancements in metallurgical techniques, such as additive manufacturing, are enabling the production of complex, high-strength components that were previously impossible to create. These advancements in metallurgy have paved the way for more efficient and safer aircraft designs. Lighter, more robust materials contribute to reduced fuel consumption, extending the range and payload capacity of aircraft.
Moreover, these new materials significantly enhance the overall aerodynamics and flight efficiency of modern aircraft. The use of innovative metallurgical methods such as 3D printing or additive manufacturing in aerospace engineering allows for the production of highly specialized components with precision and minimal waste.
This technological leap not only boosts performance but also cuts costs and production times, propelling the aerospace industry into a new era of innovation.
Construction and Infrastructure
In the realm of construction and infrastructure, metallurgical innovations contribute to the development of more robust and more resilient structures, often utilizing copper and other alloys. Steel, in particular, is a cornerstone material due to its superior tensile strength, durability, and versatility, usually produced through advanced smelting processes in the furnace.
Modern metallurgical processes enhance steel’s properties, making it more resistant to environmental stresses such as corrosion, extreme weather conditions, and earthquake forces through innovative materials science.
These improved properties allow architects and engineers to design and build taller buildings, longer bridges, and more durable infrastructure, utilizing innovative physical metallurgy methods. The strength and flexibility of advanced metallurgy mean that structures can withstand more significant stress and strain, leading to a longer lifecycle and reduced maintenance costs.
Furthermore, the ability to recycle steel effectively makes it a sustainable choice for future construction projects, aligning with global efforts to minimize environmental impact and improve the properties of metals. Using recycled steel reduces carbon emissions and conserves natural resources, making it an environmentally friendly choice in construction and a prime example of effective extractive metallurgy practices.
Energy and Power Generation
Metallurgy also plays a pivotal role in energy and power generation, with advanced materials being crucial for building more efficient turbines, pipelines, and reactors, and metallurgists are continually exploring new options.
For instance, the use of improved alloy compositions in turbine blades can significantly boost the efficiency of power plants, leading to more sustainable energy production and reduced reliance on traditional Iron oxide sources. Optimized metallurgical materials, including those derived from Iron oxide, are essential in the context of renewable energy sources like wind and solar power.
High-performance metals used in wind turbine generators and solar panel mounts ensure longevity and efficiency, maximizing the output of renewable energy systems through advanced smelting techniques in the furnace.
Adapting these advanced materials helps reduce greenhouse gas emissions, optimize energy consumption, and extend the lifespan of critical energy infrastructure components, showcasing the importance of skilled metallurgists.
This directly correlates with the growing global emphasis on sustainable and renewable energy sources, ensuring that future power generation meets environmental and economic goals.
Future Trends in Metallurgy
Looking ahead, several exciting trends in materials science are expected to shape the field of metallurgy. These include developing novel materials with unparalleled properties, such as high-entropy alloys and amorphous metals, which can be derived from advanced extractive metallurgy techniques that extract metals from their ores.
High-entropy alloys are composed of multiple principal elements, offering a unique combination of strength, flexibility, and resistance to wear and corrosion, making them ideal for applications in physical metallurgy. Amorphous metals, or metallic glasses, boast exceptional strength and wear resistance due to their disordered atomic structures and unique properties of metals.
Additionally, advancements in computational metallurgy allow scientists to design materials at an atomic level, optimizing their performance for specific applications. These computational techniques enable the precise tuning of material properties, opening new possibilities in areas such as biomedical implants, electronic devices, and clean energy technologies through advanced materials science.
The emergence of these new materials and techniques promises to revolutionize various industries, providing solutions previously thought to be unattainable in powder metallurgy. From medical devices to space exploration, the future applications are expansive and inspiring, driving continued innovation and economic growth in the history of metallurgy.
Sustainable Practices in Metallurgy
Sustainability is becoming increasingly crucial in metallurgy, especially with the growing focus on recycling and the efficient extraction of metals. Efforts to recycle metals and reduce the environmental impact of metallurgical processes, including the extraction of metals from ore, are gaining traction in non-ferrous metallurgy.
By implementing greener practices, the industry aims to meet global sustainability goals while continuing to innovate and drive economic growth. From improving energy efficiency in production processes to minimizing waste, sustainable metallurgy ensures that future generations can benefit from these advancements without compromising the planet’s health.
Embracing these practices is a trend and a necessity in our journey toward a sustainable future, particularly in extractive and non-ferrous metallurgy. Technologies such as electro-slag and vacuum arc remelting help refine and purify metals, reducing waste and improving product quality.
Moreover, adopting closed-loop recycling systems ensures that metal scrap is efficiently reused, conserving valuable resources and reducing the environmental footprint.